What Is Lean Project Management?
Lean project management is the application of lean manufacturing principles to the practice of project management. The goal of lean project management is to maximize value while minimizing waste. Lean manufacturing principles were developed by Toyota in the 1950s and applied in the 1970s to combat the energy crisis. The term “lean” was coined in the late 1980s. The Project Management Institute sums it up: “To be Lean is to provide what is needed, when it is needed, with the minimum amount of materials, equipment, labor, and space.”
Lean manufacturing identifies three types of waste: muda, muri, and mura (known collectively as the 3M).
- Muda refers to activities that consume resources without providing additional value
- Muri refers to the overuse of equipment or employees
- Mura is operational “unevenness,” which decreases efficiency and productivity in the long term
Lean project management aims to reduce the 3M within the project process.
What are the benefits of lean project management?
Organizations that use lean project management can expect:
- Reduced lead times
- Lower inventory and storage costs
- Decreased overall costs
- Improved productivity and efficiency
- Greater quality
- Higher customer satisfaction
The five key principles of lean project management
First published in 1996, the book Lean Thinking by James P. Womack and Daniel T. Jones introduced five key principles that can be used to apply the lean concept to project management.
- Specify value: What is the project’s value in the mind of the customer?
- Map the value stream: A “value stream” map shows the entire process for creating the product or project. Once this process is mapped, it can be analyzed for waste, such as unnecessary steps that tax resources or compromise quality.
- Make value flow by eliminating waste: Creating an improvement plan will eliminate the waste identified in the value stream. This plan represents a “future state” for the project’s process.
- Make value flow at the customer’s demand: The ideal scenario is to move the project forward or create the product when requested by the customer. Get as close to this as possible to reduce inventory and save resources.
- Embrace continuous improvement in pursuit of perfection: Regularly reassess the project process to eliminate waste and maximizing productivity and efficiency.
Further reading:
- 3 Easy Ways to Cut Costs and Keep Your Business Lean
- Waste Not: Becoming a Lean Team Means Cutting These Wastes (Video)
- From Toyota, to AirBus, to Wrike: The Lean Journey of Errette Dunn (Podcast)
- 5 Lessons in Lean Product Development from the Wright Brothers (Infographic)
- Startups Should Lean on Lean Project Management
What Is Lean Project Management?
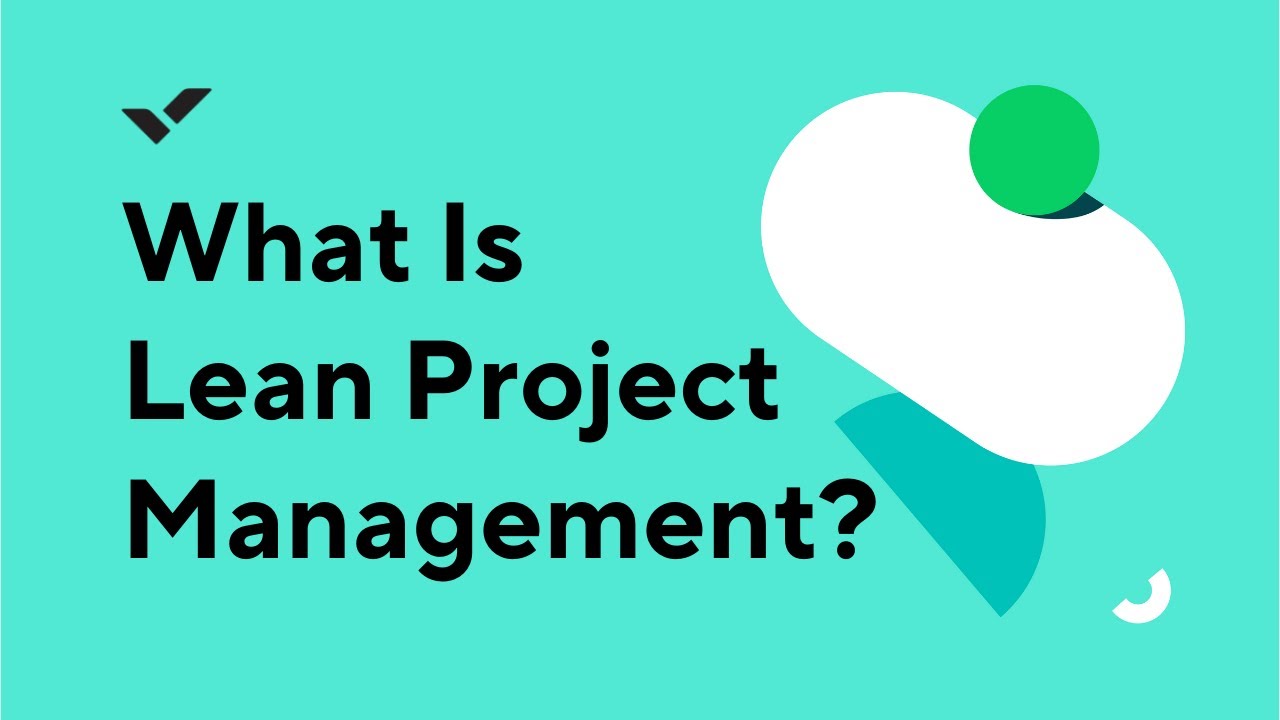
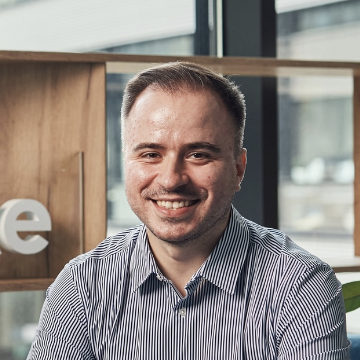
Artem Gurnov
Artem is a Director of Account Development at Wrike. He previously held the role of Project Manager, overseeing a team of customer success managers (CSMs). Over the years of building teams and scaling business processes, he has successfully deployed multiple projects, from automating client outreach to setting up work prioritization tools for sales reps and CSMs.